Top packaging machine repair service to keep your business on track.
Top packaging machine repair service to keep your business on track.
Blog Article
Exactly How Professional Packaging Equipment Fixing Solutions Decrease Downtime and Increase Performance
Expert packaging machine repair service solutions are essential in decreasing downtime and boosting performance via specialized diagnostics and prompt treatments. The effects of such services extend beyond immediate repair services-- unboxing the broader impact on operational efficiency reveals essential understandings into long-lasting efficiency methods.
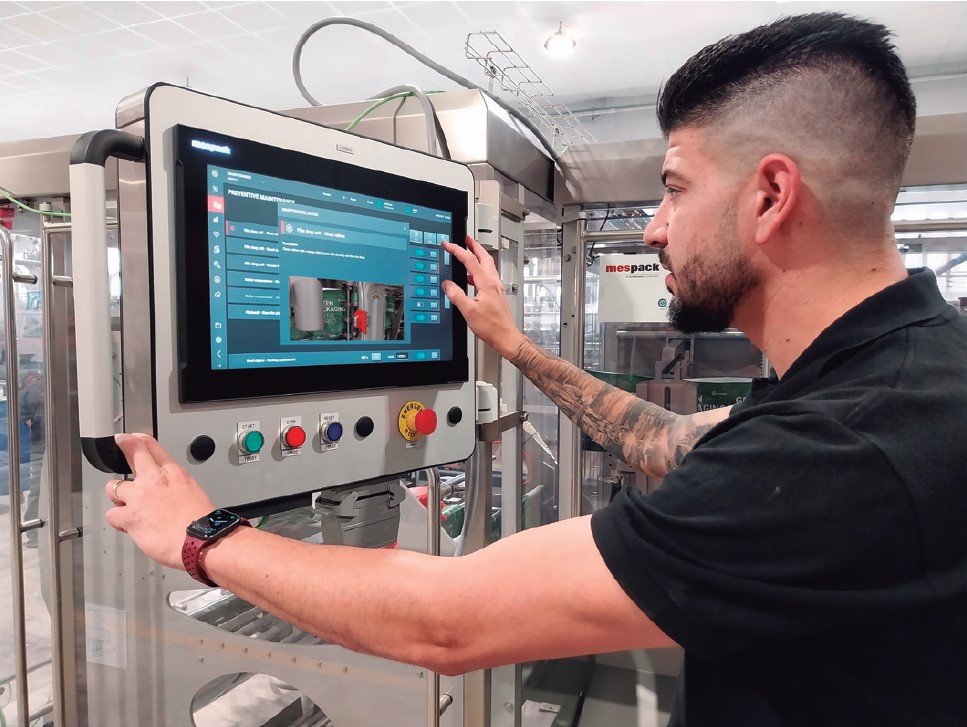
Relevance of Timely Repair Works
Prompt repairs of packaging equipments are crucial for keeping operational performance in any type of manufacturing setting. When equipment breakdowns or breaks down, it can lead to substantial disruptions in manufacturing lines, resulting in increased downtime and lost income. The longer a product packaging maker stays out of compensation, the better the impact on overall efficiency, possibly causing hold-ups in fulfilling orders and reducing client complete satisfaction.
In addition to the instant economic implications, delayed repair work can cause much more comprehensive damages to the equipment. Elements that are not attended to immediately can weaken even more, calling for even more pricey repair services or total replacements, which can have been stayed clear of through timely intervention. Normal maintenance and prompt repair work can boost the life-span of packaging devices, guaranteeing that they run at ideal efficiency levels.
Investing in specialist product packaging equipment repair solutions is necessary for minimizing these risks. A positive strategy to fixings not only preserves production timetables but additionally cultivates a society of reliability within the organization. By focusing on timely repair work, services can preserve their one-upmanship, maximize source allowance, and eventually enhance their lower line with boosted operational performance.
Expertise in Diagnostics
When it pertains to keeping the effectiveness of packaging machines, proficiency in diagnostics plays an essential duty in identifying concerns prior to they rise into significant failures. Skilled technicians utilize sophisticated analysis tools and strategies to perform detailed analyses of device efficiency. This proactive technique allows them to identify the origin causes of malfunctions, whether they originate from mechanical wear, electrical mistakes, or software discrepancies.
Efficient diagnostics not only promote speedy identification of issues however also improve the overall integrity of packaging procedures. By performing extensive analyses, professionals can assess the wellness of essential components, guaranteeing that also minor irregularities are resolved without delay. This focus to detail decreases the risk of unanticipated failures, which can cause expensive downtime.

Preventive Upkeep Advantages
Preventative maintenance matches professional diagnostics by proactively resolving possible issues prior to they materialize right into significant troubles. By applying a structured preventive upkeep program, companies can dramatically lower the threat of unforeseen equipment failures, therefore decreasing pricey downtime. Routine examinations, cleaning, and components substitute aid guarantee that product packaging machinery operates at optimum efficiency.

In addition, preventive upkeep contributes to improved safety and security conditions within the office. By recognizing and remedying prospective dangers before they intensify, companies create a safer environment for their staff members. This aggressive strategy not only shields workers yet additionally cultivates a society of duty and alertness.
Last but not least, regular preventive upkeep can boost item quality. Well-maintained devices runs more continually, lowering the probability of issues and making sure that packaging fulfills rigorous market criteria. In recap, preventative maintenance is an essential strategy for maximizing productivity and guaranteeing operational excellence.
Custom-made Service Solutions
Acknowledging the special demands of each service, tailored solution options for packaging maker repair work deal customized approaches that enhance operational performance. These services are developed to attend to certain challenges encountered by various markets, making certain that machine downtime is minimized and efficiency is taken full advantage of.
Expert repair work services begin with a detailed evaluation of a company's packaging procedures. By recognizing the details equipment included and the Recommended Reading needs of the manufacturing setting, specialists can develop a personalized upkeep and repair work strategy. packaging machine repair service. This may consist of specialized training go for internal team, the application of anticipating maintenance technologies, or the stipulation of dedicated support during optimal production times
Moreover, personalized options can incorporate adaptable solution agreements that line up with a business's operational timetable, enabling for repairs to be carried out throughout off-peak hours. By prioritizing the unique requirements of each business, these custom services make certain that repairs are not just efficient yet likewise perfectly integrate into existing operations.
Eventually, the concentrate on personalization allows firms to maximize their packaging procedures, leading to enhanced integrity and efficiency of equipment, which is vital for keeping affordable benefit in today's busy market.
Effect On Overall Effectiveness
Personalized service remedies not just address particular fixing requirements but also play a considerable function in boosting general operational effectiveness. By giving targeted interventions, specialist product packaging device repair service services straight decrease the frequency and duration of devices failings. This proactive strategy makes sure that manufacturing lines continue to be operational, minimizing interruptions that can cause costly downtime.
Furthermore, reliable repair service solutions add to smoother operations, as well-kept machinery operates at ideal performance degrees. When devices operate properly, the top quality of packaged items improves, leading to less problems and much less rework. This enhancement not only increases productivity however additionally enhances client complete satisfaction.
In addition, normal maintenance and quick feedback times from repair service professionals foster a culture of integrity within the company. Staff members can concentrate on their main jobs instead of stressing over potential tools breakdowns. The general throughput of the manufacturing process increases, enabling business to meet need much imp source more properly.
Ultimately, the critical financial investment in professional repair service solutions translates to enhanced efficiency across all functional facets, ensuring that services can adapt and grow in an open market. This harmony in between upkeep and productivity is vital for lasting success.
Conclusion
In conclusion, expert packaging device repair work solutions play a vital function in minimizing downtime and boosting productivity within producing settings. Timely repairs, specialist diagnostics, and preventive maintenance contribute to the integrity of tools, while tailored service solutions attend to specific functional needs.
Report this page